Basic Feature
- Home
- Basic Feature
Feature of Injection Moldin Mchine
Injection molding machines are versatile manufacturing tools used to produce a wide range of plastic parts and products. The features of these machines can vary based on their type, size, and manufacturer. Here are some common features found in injection molding machines:
Clamping Unit:
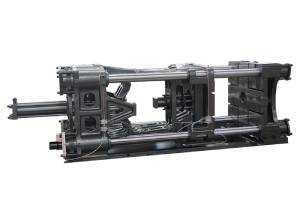
- Clamping Force: The force applied to hold the mold closed during injection.
- Mold Opening/Closing Mechanism: How the mold halves are opened and closed.
- Platen Size: The dimensions of the clamping plates holding the mold.
Injection Unit:
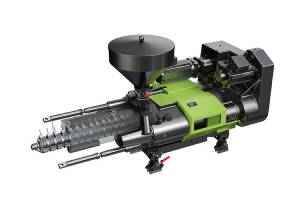
- Injection Rate: The speed at which the molten plastic is injected into the mold.
- Screw Design: Different screw types for various materials and applications.
- Injection Pressure: The pressure applied to inject the plastic into the mold cavity.
- Barrel Heating Zones: Multiple heating zones for precise temperature control.
Control System:
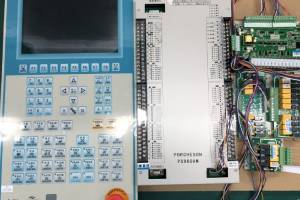
- Programmable Logic Controller (PLC): Controls and monitors the machine’s operation.
- Human-Machine Interface (HMI): Touchscreen interface for user interaction.
- Process Control: Monitors and adjusts parameters like temperature, pressure, and cycle time.
Hydraulic System:
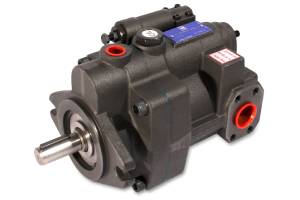
- Hydraulic Pump: Generates hydraulic pressure for the clamping and injection processes.
- Hydraulic Valves: Control the flow of hydraulic fluid to different components.
- Accumulator: Stores hydraulic energy for quick responses during high-demand phases.
Mold System:
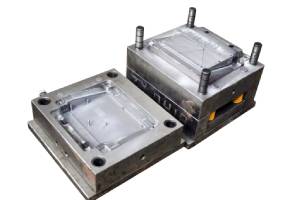
- Cooling System: Channels within the mold to regulate the temperature.
- Ejector Mechanism: Mechanism to push the finished part out of the mold.
- Runner System: Channels guiding molten plastic from the injection unit to the mold cavities.
Electrical Panel:
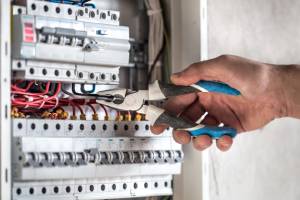
- Control System: The electrical panel in an injection molding machine contains the control system.
- Heating and Cooling Systems: The electrical panel houses components responsible for controlling the temperature of the injection molding process.
- Safety Systems: Safeguards against excessive pressure in the hydraulic system.
Motor & Drive:
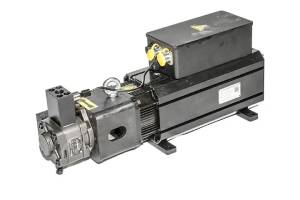
- Energy Efficiency: Servo systems consume power based on the actual needs of the machine, reducing energy waste.
- Precision and Accuracy: Servo motors and drives offer precise control over speed, position, and torque, leading to accurate molding processes.
Lubrication Systems:
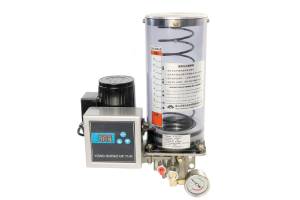
- Selection of Grease: Choose high-quality grease based on operating conditions.
- Lubrication Points: Identify and lubricate bearings, guide rails, screws, and moving parts.
- Automatic Lubrication Systems: Consider systems for precise, scheduled grease delivery.
Material Handling:
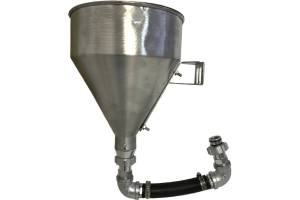
- Hopper: Holds and feeds raw plastic material into the injection unit.
- Dryer: Removes moisture from plastic pellets to ensure quality molding.