Products
- Home
- Products
Injection Molding Machine
Introduction
Injection molding machines play a vital role in modern manufacturing, enabling the cost-effective and efficient production of a wide range of plastic products.
Purpose
Injection molding machines are specialized devices designed to melt plastic and inject the molten material into a mold cavity. Once the plastic cools and solidifies within the mold, it takes on the mold’s shape, resulting in a finished product.
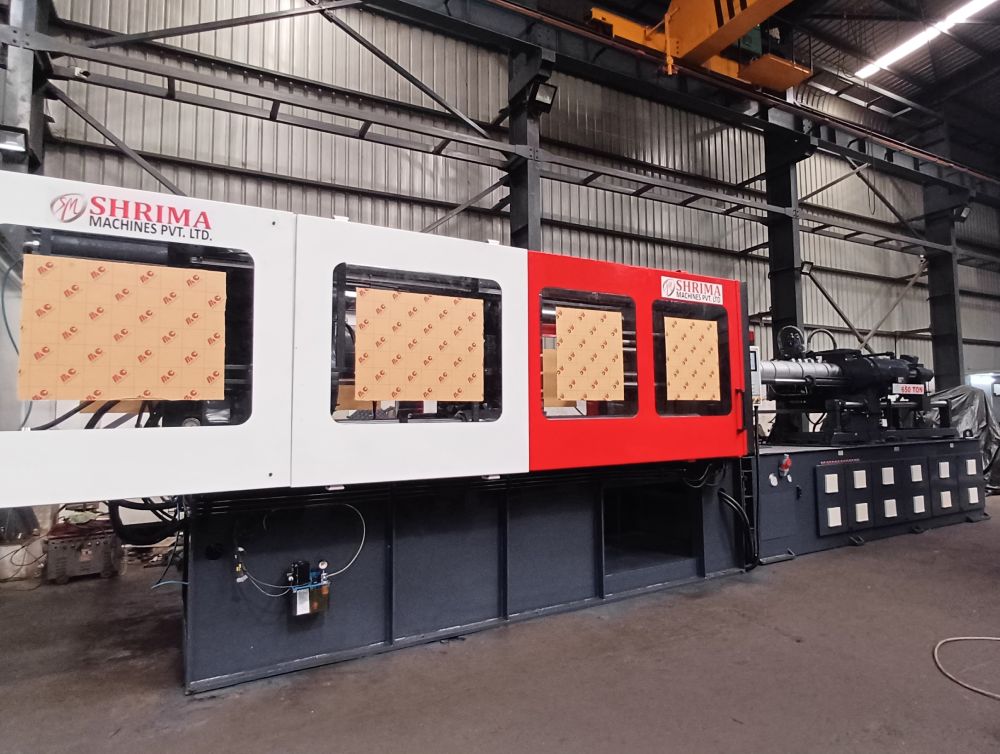
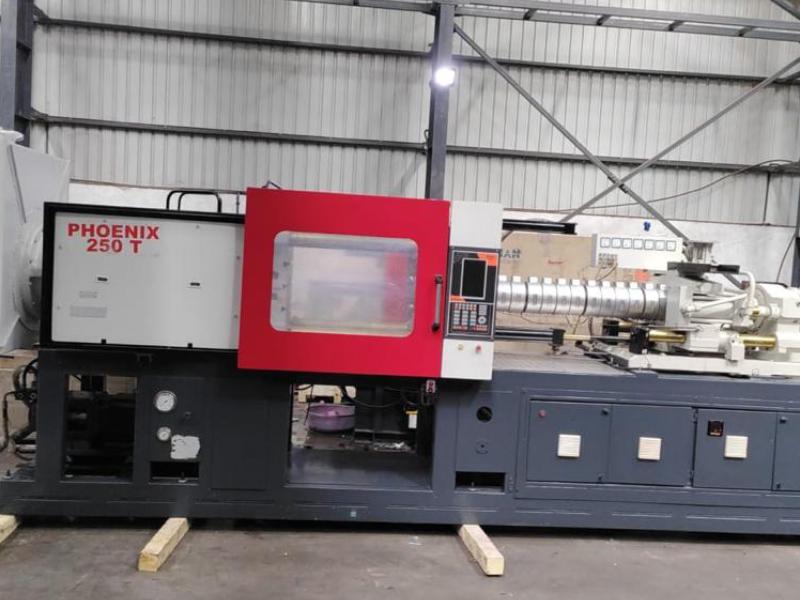
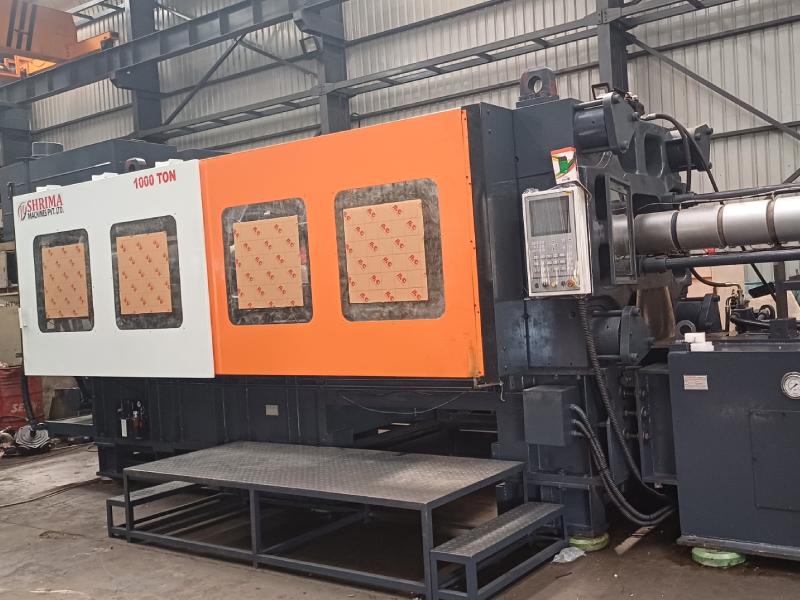
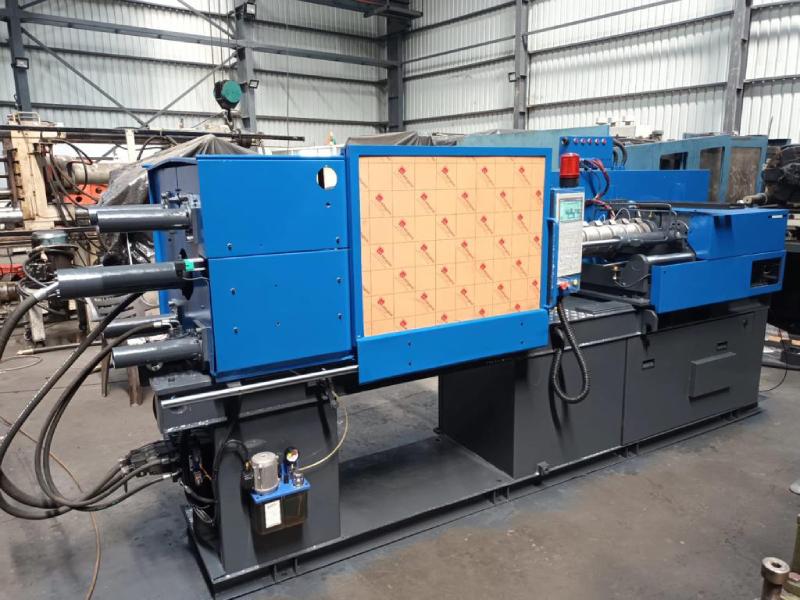
Find informative answers to all your questions about Industrial products below.
An injection molding machine is a manufacturing tool used for producing plastic parts through the injection molding process. It consists of a material hopper, an injection unit, a clamping unit, and a control unit.
The process involves melting plastic resin and injecting the molten material into a mold cavity. Once the plastic cools and solidifies, the mold opens, and the finished part is ejected.
A wide variety of thermoplastics can be used, including but not limited to polyethylene, polypropylene, polystyrene, polyvinyl chloride (PVC), and engineering plastics like ABS, PC, and nylon.
Key components include the material hopper, injection unit, screw or Ring plunger, mold cavity, clamping unit, and the control system.
The mold is typically cooled by water channels within its structure. Coolant is circulated to dissipate heat and solidify the plastic.
Common challenges include flash (excess material at parting lines), sink marks, warpage, and issues related to material flow and temperature control.
Consider factors such as the type of material, part size and complexity, production volume, and required precision. Consulting our experts and machine suppliers can help in making the right choice.
All types of injection molding machinery, service & spare parts related question to connect with us
Injection molding machines are categorized based on their clamping force, which is the force required to hold the mold closed during the injection and cooling processes. The clamping force is typically measured in tons. Here’s a breakdown of the categories you mentioned:
50 Ton to 300 Ton:
- Small to medium-sized machines.
- Suitable for molding smaller parts and products.
- Examples: Medical components, consumer goods, small automotive parts.
350 Ton to 450 Ton:
- Medium-sized machines.
- Can handle a broader range of part sizes.
- Applications: Larger consumer goods, automotive components, medium-sized industrial parts.
500 Ton to 1000 Ton:
- Large machines with high clamping force.
- Used for manufacturing larger and more complex parts.
- Applications: Large automotive components, industrial containers, appliance parts.
These categories represent a general classification based on clamping force, but it’s important to note that specific applications and requirements can vary. Manufacturers often choose the appropriate machine size based on the size and complexity of the parts they intend to produce. Additionally, advancements in technology may lead to changes in machine specifications and classifications over time.